
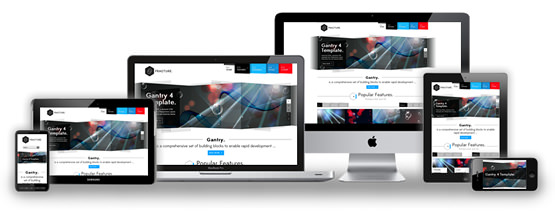
In this system, an inflatable elastomeric bladder is sheathed with a double helical fiber weave. Using materials and fabrication technologies available since the 1950s, the so-called McKibben’s artificial muscle is one of the earliest examples of pneumatic soft actuators that can achieve large contractile and extensional deformations 7. Despite such encouraging developments, further research in materials and fabrication technologies is needed to enable seamless manufacturing of soft actuators that reach the level of motion control observed in biological systems 6. FEAs inspired by octopus, worms, and starfish have been shown to perform tasks that would not be possible with hard structures 1. Air- and liquid-driven actuators, also known as fluidic elastomer actuators (FEAs), are particularly interesting because of their simple control without the need of many active components 5. In contrast to the mechatronic control of conventional actuation systems, soft actuators can be driven by heat, light, air pressure, or liquid displacement. Besides conformability and complex motion, low weight and reduced energy consumption are other major advantages of soft actuators compared to conventional rigid counterparts. Soft actuators enable smooth and conformable complex motions that ensure safe interactions of robots with humans and have led to impressive assistive technologies for rehabilitation and training 1, 2, 3, 4. Exploring such programmability enables 3D printing of a broad range of soft morphing structures. Using a quantitative model based on lamination theory, we establish design principles for the digital fabrication of silicone-based soft actuators whose functional response is programmed within the material's properties and architecture.

Similar to the fibrous architectures found in muscular hydrostats, the lead angle can be altered to achieve elongation, contraction, or twisting motions. The actuators comprise an elastomeric body whose surface is decorated with reinforcing stripes at a well-defined lead angle. Here, we report a 3D printing platform for the seamless digital fabrication of pneumatic silicone actuators exhibiting programmable bioinspired architectures and motions.
#Using responsive grids in gantry hydrogen full#
Full exploitation of the potential of soft actuators has, however, been hindered by the lack of simple manufacturing routes to generate multimaterial parts with intricate shapes and architectures.
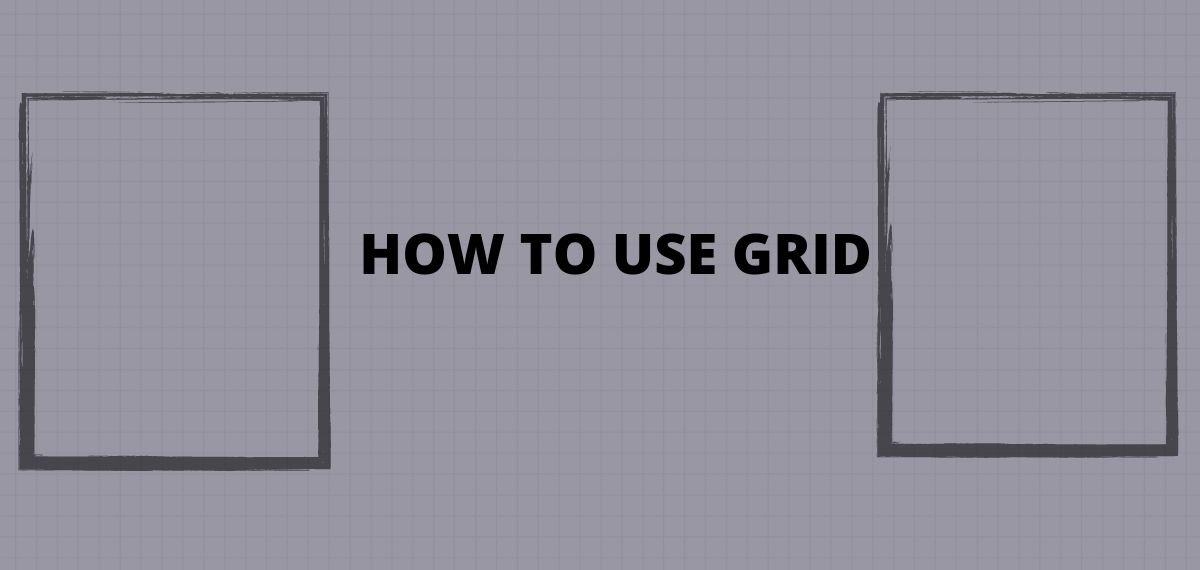
Soft actuation allows robots to interact safely with humans, other machines, and their surroundings.
